They are finally preparing to repair the gaping hole in Davis Besse's head.
Press release from plant owner:
New reactor head arrives at Davis Besse nuclear power plant
Akron, Ohio, November 29, 2010 — FirstEnergy Nuclear Operating Co., a unit of FirstEnergy Corp., announced that the new reactor head for the Davis-Besse Nuclear Power Station in Oak Harbor, Ohio, has been off-loaded at the Port of Cleveland and will be transported by truck to the plant next week.
Final work on the reactor head was completed in France, including the installation of control rod drive mechanism nozzles made of material less susceptible to cracking under high temperatures and pressures.
The head measures nearly 17 feet in diameter, is eight-feet tall and weighs more than 82 tons. A comprehensive pre-service inspection was conducted by FENOC personnel before the head was shipped from Antwerp, Belgium, on November 5.
The new reactor head will be placed in a specially constructed building at Davis-Besse where new control rod drive mechanisms and other components will be fitted before installation takes place in the fall of 2011.
FirstEnergy is a diversified energy company headquartered in Akron, Ohio. Its FENOC subsidiary also operates the Beaver Valley Power Station in Shippingport, Pennsylvania, and the Perry Nuclear Power Plant in Perry, Ohio.
What they'd rather not discuss:
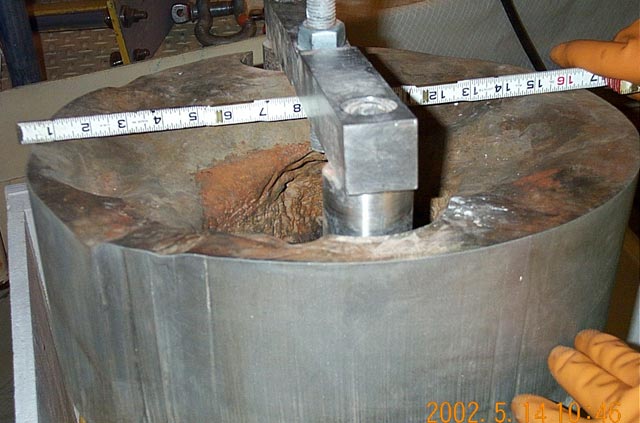
The reactor core at the Davis-Besse nuclear plant sits within a metal pot designed to withstand pressures up to 2,500 pounds per square inch. The pot -- called the reactor vessel -- has carbon steel walls nearly six inches thick to provide the necessary strength. Because the water cooling the reactor contains boric acid that is highly corrosive to carbon steel, the entire inner surface of the reactor vessel is covered with 3/16-inch thick stainless steel.
But water routinely leaked onto the reactor vessel's outer surface. Because the outer surface lacked a protective stainless steel coating, boric acid ate its way through the carbon steel wall until it reached the backside of the inner liner. High pressure inside the reactor vessel pushed the stainless steel outward into the cavity formed by the boric acid. The stainless steel bent but did not break. Cooling water remained inside the reactor vessel not because of thick carbon steel but due to a thin layer of stainless steel. The plant's owner ignored numerous warning signs spanning many years to create the reactor with a hole in its head.
Workers repairing one of five cracked control rod drive mechanism (CRDM) nozzles at Davis-Besse discovered extensive damage to the reactor vessel head. The reactor vessel head is the dome-shaped upper portion of the carbon steel vessel housing the reactor core. It can be removed when the plant is shut down to allow spent nuclear fuel to be replaced with fresh fuel. The CRDM nozzles connect motors mounted on a platform above the reactor vessel head to control rods within the reactor vessel. Operators withdraw control rods from the reactor core to startup the plant and insert them to shut down the reactor.
The workers found a large hole in the reactor vessel head next to CRDM nozzle #3. The hole was about six inches deep, five inches long, and seven inches wide. The hole extended to within 1-1/2 inches of the adjacent CRDM nozzle #11. The stainless steel liner welded to the inner surface of the reactor vessel head for protection against boric acid was at the bottom of the hole. This liner was approximately 3/16-inch thick and had bulged outward about 1/8-inch due to the high pressure (over one ton per square inch) inside the reactor vessel.
What could have happened?
A loss-of-coolant accident (LOCA) occurs if the stainless steel liner fails or CRDM nozzle #3 is ejected. The water cooling the reactor core quickly empties through the hole into the containment building. The containment building is made of reinforced concrete designed to withstand the pressure surge from the flow through the break.
To compensate for the reactor water exiting through the hole, water inside the pressurizer (PZR) and the cold leg accumulators flows into the reactor vessel. This initial makeup is supplemented by water from the Refueling Water Storage Tank (RWST) delivered to the reactor vessel by the high, intermediate, and low pressure injection pumps. The makeup water re-fills the reactor vessel and overflows out the hole in the reactor vessel head. Approximately 30 to 45 minutes later, the RWST empties. Operators close valves between the pumps and the RWST and open valves between the low pressure injection (RHR) pumps and the containment sump. Water pouring from the broken reactor vessel head drains to the containment sump where the RHR pumps recycle it to the reactor vessel. A cooling water system supplies water to the RHR heat exchanger shown to the left of the RHR pump to remove heat generated by the reactor core.
On paper, that's how the safety systems would have functioned to protect the public. But the following examples suggest that things might not have gone by the book:
-The Three Mile Island nuclear plant experienced a loss of coolant accident in March 1979. Emergency
pumps automatically started to replace the water flowing out the leak. Operators turned off the pumps
because instruments falsely indicated too much water in the reactor vessel. Within two hours, the reactor
core overheated and melted, triggering the evacuation of nearly 150,000 people.
-At the Callaway nuclear plant in 2001, workers encountered problems while testing one of the emergency
pumps. Investigation revealed that a foam-like bladder inside the RWST was flaking apart. Water carried
chunks of debris to the pump where it blocked flow. The debris would have disabled all the emergency
pumps during an accident.
-At the Haddam Neck nuclear plant in 1996, the NRC discovered the piping carrying water from the RWST
to the reactor vessel was too small. It was long enough but it was not wide enough to carry enough water
during an accident to re-fill the reactor vessel in time to prevent meltdown. The plant operated for nearly 30
years with this undetected vulnerability.
-At several US and foreign nuclear power plants, including the Limerick nuclear plant 8 years ago, the force
of water/steam entering the containment building during a loss of coolant accident has blown insulation off
piping and equipment. The water carried that insulation and other debris into the containment sump. The
debris clogged the piping going to the emergency pumps much like hair clogs a bathtub drain. According to
a recent government report, 46 percent of US nuclear plants are very likely to experience blockage in the
containment sumps in event of a hole the size found at Davis-Besse opens up. For slightly larger holes, the
chances of failure increase to 82 percent.<1>
Thus, events at Davis-Besse may have gone by the book had the stainless steel failed it would have become the subject of many books on the worst loss of coolant accident in US history...
UCS -- Aging Nuclear Plants -- Davis-Besse: The Reactor with a Hole in its Head
http://www.ucsusa.org/assets/documents/nuclear_power/acfnx8tzc.pdf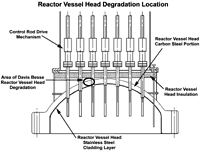
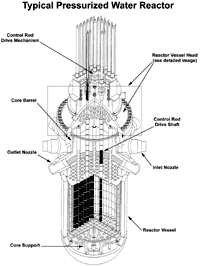
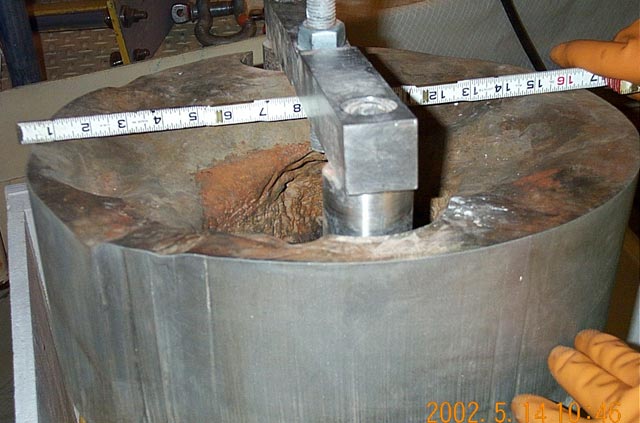
Scapegoating of Davis Besse by NRC
http://www.ucsusa.org/news/press_release/federal-agency-scapegoating-0141.htmlRetrospective
http://www.ucsusa.org/nuclear_power/nuclear_power_risk/safety/davis-besse-retrospective.html