A Not-So-Brief Primer on Aircraft De-icing and Anti-icing: From Ground Thingys to “Weeping Wingys.”Basic terminologyDe-icing refers to ice removal. Anti-icing refers to the prevention of airframe and power-plant ice accumulation. De-icing and anti-icing can be functions of aircraft systems (in-flight) or ground operations.
In-flight icing protection can be as simple as climbing or descending to warmer, ice-melting air when icing conditions have been encountered (de-icing), or – better yet - studiously avoiding known in-flight icing conditions (the most basic form of anti-icing, to include a no-go decision before takeoff). Or, in-flight protection can be as complicated as the “weeping wing” system favoured by certain British aircraft manufacturers.
BTW: Just because your new Cirrus or Beechcraft Baron has de-ice/anti-ice equipment does NOT mean that you are legal to blast off into known icing conditions. Such equipment is like a parachute: there for escape, not for daily use.
I’m often asked questions
such as, “How much ice
can a Cessna 172 carry?”
How much an airplane
can or cannot carry isn’t
the question. The real
question is, “Does the
FAA say the airplane can
be flown in ice?” If it
isn’t ice approved, then
you don’t have any
business flying it in ice.
-Capt. Robert Buck,
Author of “Weather Flying”
Ground operationsAlmost anyone who has ever flown on the airlines during the winter has seen ground de-icing operations being performed. The aircraft is sprayed with a hot propylene glycol brew known as type-I deicing fluid. Type-I de-icing fluid melts the ice/snow (or even frost) that might be adhering to the exterior surfaces of the aircraft. If no frozen precipitation is still falling after de-icing on the ground, the aircraft is usually good to go. If frozen goo is still coming down, the captain must request a bath of type-IV de-icing fluid (or type-II if type-IV is not available). There is a type-III fluid, designed for slower aircraft (with takeoff speeds less than 100 knots or 115 mph).
Type-IV fluid has both de-icing and anti-icing capabilities. Hot type-IV “de-ices” like type-I, but unique chemical properties of the type-IV fluid provide anti-ice protection for a “holdover time” that is determined by the captain from a chart in the cockpit (function of temperature, precipitation intensity, and time). Those chemical characteristics of type-IV fluid are usually modified with the kick-ass adjectives “thixotropic” and “pseudoplastic” (referring to polymeric thickening agents), which basically says that the fluid will adhere to the aircraft surfaces for a while, even during takeoff, providing anti-icing protection until the aircraft systems can takeover. Not that it should ever matter (and it never mattered when I was in command), but it should be noted that type-4 fluid is much more expensive than type-I fluid.
In-flight anti-ice (pro-active) and de-ice (re-active)Most aircraft with an electrical system, which is to say almost anything flying, has a basic anti-icing system: pitot heat. The pitot-static system is electrically heated in a Cessna 150 as well as a Boeing 747. It works upwards from there (gets more complex).
In a jet transport aircraft certain anti-icing systems are turned on well before takeoff and remain on until at the gate after landing, even in CAFB (Clear And Friggin’ Beautiful) weather. An inoperative pitot-static heating system is a “no-go” item. It must be on and working to fly. Period.

Electrically heated pitot tube on a Cessna aircraft
Inoperable windshield heat on jet transport aircraft is
not a “no-go” item (it can be “MELed” – flown with until repaired - with certain restrictions on flight), but perhaps it should be required for all flight (and I think Capt. “Sully” Sullenberger would agree with me on this). The laminated windshields of most airline-type jets are heated by “wild-AC” (wild frequency alternating current). I have never, IIRC, seen ice form on a jet’s heated windshield (windshield wipers are another story, and they are the proverbial canary in the ice mine - so to speak). But the lagniappe associated with this type of windshield heat – that 13th donut when you order a dozen – is the extra measure of bird-strike protection that a heated (and malleable) laminated windshield has over an un-heated (and brittle) windshield. I know. I took a direct duck-strike on the heated windshield of a Boeing 737-300 without as much as a scratch on the glass.
A myriad array of de-icing and anti-icing systems protects flying contraptions the world over. Some aircraft have sophisticated in-flight ice detection systems. Some have not-so-sophisticated ice detection systems. The best ice detection system on the Boeing 737 is pilot eyes watching for ice buildups on the windshield wipers (with the help of a flashlight at night).
The British engineers came out with the weird “weeping wing” approach to anti-icing protection on the HS-125 Hawker jet series (an perhaps others). An anti-icing fluid, known by the proprietary name of TKS Fluid (don’t ask, nobody will tell you or me what “TKS” means) is carried in a reservoir and pumped to the wing and tail leading edges where it is exuded through a porous mesh surface. The TKS system should be activated before ice accumulates on the aircraft, or else the ice might obstruct the mesh delivery system. The TKS concept seems to be catching on with smaller aircraft manufacturers, like the Cirrus. That’s all I know about “weeping wings”.

TKS fluid exuding from mesh leading edge
Then there are the de-icing “rubber” boots. De-icing boots are pneumatic devices affixed to wing and tail leading edges. They are inflated periodically after icing conditions have been encountered to break off the ice once it has formed. Some de-icing boot systems are purely manual, and some have automatic features including ice detectors and timers. I have flown a few prop airplanes with rubber boots. I used them judiciously and never had a problem. I also flew the Lockheed JetStar-II, one of the few swept-wing jets with de-icing boots. I never ever saw ice on the JetStar wing, probably because of the heat of compressibility at the speeds we flew (and our studious avoidance of icing conditions). Don’t forget ‘yer rubbers!
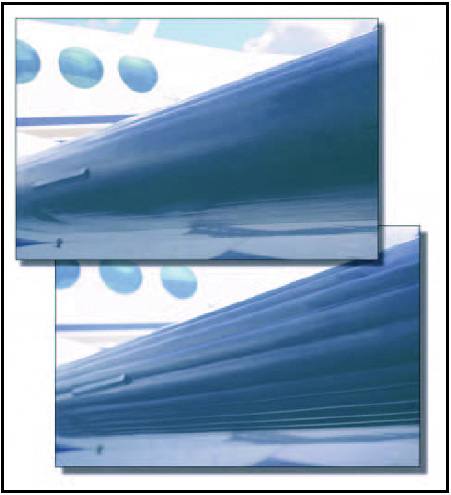
The Dash-8-400 at Buffalo had similar de-icing boots
Propeller anti-ice/de-ice systems range from electrically heated “blankets” on the prop leading edge to anti-icing fluids that are pumped and squirted from the prop spinner onto channels on the propeller leading edge. Modern turboprop aircraft, like the Q-400 that crashed at Buffalo, usually use a combination of electro-thermal heating elements (windshield, pitot-static, props) and pneumatic boots (wing and tail leading edges) for in-flight icing protection.
Bleed Air: Best Protection (Short of Icing-Abstinence)A turbojet or turbofan engine has a ready-made heat and pressure source within: the jet motor’s compressor section. Air, at very high pressures and very high temperatures, is tapped (“bled”) from the jet engine’s compressor section (thus the term, “bleed air”), cooled, and put to work elsewhere in the airplane. An air cycle machine extracts energy from the air and pumps it into the aircraft cabin (the “pressure vessel”) for pressurization and warm/cool conditioned air. Some of the hot, compressed air is used by the airframe (wing and tail) and engine anti-ice systems.
Engine anti-icing is more critical than airframe ice protection, since the engines must always continue to produce rated thrust, bleed air, and electrical power (engine-driven electrical generators). Critical engine components such as the air inlet leading edge, the turbine engine inlet guide vanes, and performance-related measurement probes are protected by hot bleed air from the engine compressor.
In my opinion, there is no better system of anti-ice protection than a hot bleed air system. Hot bleed air, ducted to airframe parts such as the wing and tail leading edges, will keep ice from forming in all but the worst imaginable icing conditions. Partial system failures are exceedingly rare, and total failures are rarer still. Unfortunately, bleed air anti-ice systems are not available on piston and most turboprop-powered aircraft.
There’s a lot more to the subject than what I’ve posted here. Feel free to add to my tome or point out any errors. This was written pretty much off the top of my head. I hope it helps to clarify some misconceptions that are being generated by media reports of the Buffalo accident. This is by no means an analysis of that accident or a commentary on that crews’ performance. I leave that in the able hands of the NTSB.
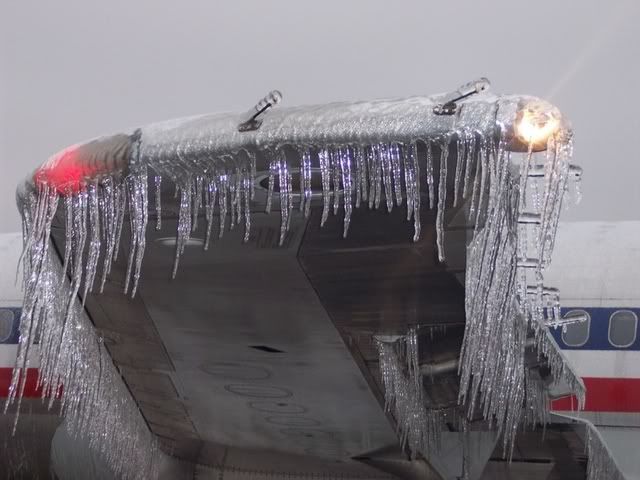